Normally, integrating external axes with a Universal Robots cobot involves relying on traditional solutions such as PLCs, HMIs, or custom software development. This increases system complexity and leads to longer commissioning times.
MAD Controller helps address these challenges by offering direct integration between the UR cobot and external axes. It is a URCap installed directly on the robot’s controller, allowing the operator to manage up to four additional axes through the same cobot interface. This enables configuring, teaching points, defining travel limits, and executing movements directly from the teach pendant—without switching environments or depending on external devices.
The system is compatible with FESTO controllers (CMMP-AS, CMMP-AS/ST), facilitating the control of linear axes used in applications such as palletizing or gantries, as well as rotary tables for dispensing, inspection, or assembly processes. Additionally, MAD Controller is designed to adapt to modular architectures requiring synchronized or asynchronous movements, enabling the execution of complex trajectories.
Benefits Compared to Traditional Solutions
MAD Controller | Solution with PLC/HMI | |
Programming | Not required (uses PolyScope and URScript) | Required (PLC + HMI programming) |
Integration Time | Fast | Slow |
Additional Hardware | Not required | Yes (PLC, HMI, I/O modules, wiring) |
Control Interface | Directly on the UR Teach Pendant | External interface (HMI or SCADA) |
Scalability | Up to 4 axes, integrated within the URCap | Limited according to architecture and licenses |
Aplicaciones prácticas con mad controller
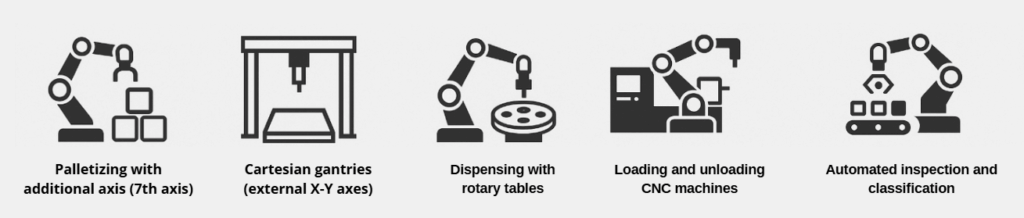
More information: https://nutai.com/en/accessories-for-ur/mad-controller/